OPC UA
Quick Guide to OPC UA and Advantech IT/OT Convergent Solutions
OPC UA, which stands for Open Platform Communications Unified Architecture, is a single service oriented architecture that provides everything needed for the transport and interpretation of data and information from first-tier control devices through to the enterprise information systems.
Learn why OPC UA is an accelerator for Industry 4.0 and the industrial internetof things, and learn where the technology is likely to lead in the future.
Table of Contents
> Video: OPC UA- more than just another protocol
> Quick Guide to OPC UA- 12 FAQs
01. What customer challenges does OPC UA address?
02. What is OPC UA and what does OPC UA stand for?
04. What are the benefits of OPC UA?
05. How is OPC UA different from other protocols such as DDS, AMQP or MQTT?
06. How does OPC UA drive industry 4.0?
07. How does OPC UA compare to other industry standards regarding cost/revenue?
08. What are OPC UA’s major applications?
09. How widely adopted is OPC UA?
10. What are the benefits of OPC UA Ethernet I/O vs. Modbus Ethernet I/O?
11. How does OPC UA enable and simplify remote facility management?
> Advantech OPC UA applications
> Advantech OPC UA product offerings
OPC UA- More Than Just Another Protocol
In this video, you will quickly learn how OPC UA benefits your business.
- Who are the OPC Foundation and what do they do
- Why OPC UA is more than ‘just another protocol’, and how it enables IT-OT convergence
- How to integrate legacy devices into an OPC UA framework
Quick Guide to OPC UA- 12 FAQs
What customer challenges does OPC UA address?
OPC UA provides a unified architecture and lexicon to define field items, the devices that interface to them and the communications between them. It enables the free flow of information between systems in a manner that allows not only the data, but also the source of the data to be defined and understood. It achieves this in an extremely secure way, providing high levels of trust and resilience in the retrieved information. As such it is highly relevant to customers:
- Seeking to integrate information from diverse device types into a complete system
- Optimizing end-to-end operations rather than individual, discrete processes
- Trying to bridge the divide between IT and OT environments
What is OPC UA and what does OPC UA stand for?
OPC is an acronym for Open Platform Communications. A number of interoperability specifications have been released over the years and in its latest iteration, OPC UA (Open Platform Communications Unified Architecture) integrates all this functionality into a single service oriented architecture. At the same time, it adds essential new features such as platform independence, diagnostics, discovery, rendering of complex information models, security, and reliability. It also provides everything needed for the transmission and interpretation of data and information from the factory or enterprise information system. OPC UA was released as an IEC Standard, IEC 62541 in October 2011.
Why is OPC UA important?
The OPC UA standard brings plug-and-play connectivity to industrial automation. Before OPC UA, application vendors had to develop custom software for every third-party device and application that needed to be integrated into the automation system. OPC UA instead offers open connectivity across products, independent of the hardware or software platforms involved. OPC UA defines a standard way for sharing real-time data, historical data, and alarms & events, reducing integration and total life cycle cost for system implementation.
What are the benefits of OPC UA?
- Object definition library provides contextualized information, not raw data, which enables true interoperability ‘out of the box’ across multiple vendors and device/applications
- Standardized information enables efficient asset performance management
- Open ecosystem avoids vendor lock-in
- Vendors differentiate by additional features and quality; not by proprietary restrictions
- End to end security model allows use across multiple communications networks
- Specifications, sample code etc. are all openly and freely available. No royalties to pay on any runtimes. Membership of the OPC Foundation is not necessary to access resources or certification labs. Modern IPR policy protects not only OPC foundation members, but also all adopters of OPC UA
- Companion specifications can be developed for devices and IT applications and services, providing a single architecture within which both OT and IT systems can interact in a common manner
How is OPC UA different from other protocols such as DDS, AMQP or MQTT?
The first thing to understand is that OPC UA is more than just a protocol. Protocols such as DDS, AMQP or MQTT are concerned with the transfer of data between applications, devices and systems. They achieve this with different levels of intrinsic security, but they do not implicitly provide any context for the data being transferred. Instead, it is up to the user to define the content of the data and because of this, it does not guarantee that the transferred data can be interpreted by a receiving system.
OPC UA addresses this by including definitions not only of data and information types, but also of the device or application which generated the data using a common object definition library (OPC UA refers to these as ‘companion specifications’). Because of this, any system implementing the OPC UA architecture is guaranteed to be able to natively connect to and interpret data from any device which supports the same companion specs.
In addition to this common object library, OPC UA also addresses security from an end-to-end perspective. As such it can be used with multiple transfer protocols including both client-server and pub-sub protocols like MQTT whilst maintaining data and user security independently of the transport layer.
How does OPC UA drive industry 4.0?
For industry 4.0 to be fully realized, there are several key issues that must be addressed, namely security, interoperability, real time operation and IT-OT integration. OPC UA provides features which address each of these requirements within a single unified architecture model:
- Security
OPC UA provides end to end security, starting with a hardware root of trust within devices, and extending through the transport, application and user security levels. All devices within a system are authenticated, and all communications are signed and encrypted.
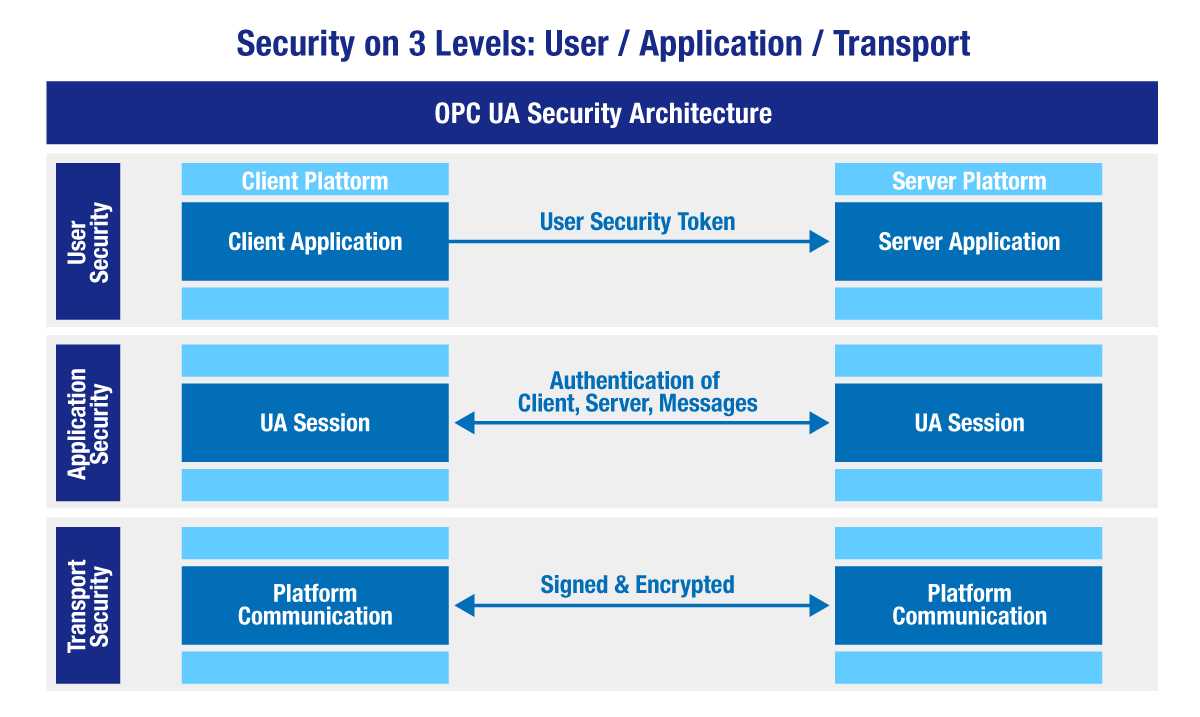
- Interoperability
OPC UA provides definitions not only of data fields and types, but also how combinations of those data fields are joined into an object which models a real device. Sharing these object definitions allows authorized OPC UA applications and devices to not only recover data, but also to interpret it without human intervention. Devices conforming to an OPC UA companion specification, for example ‘a robot’ can be freely mixed and matched within a system irrespective of manufacturer or specific characteristics such as degrees of freedom etc.
- Real Time Operation
In addition to offering pub-sub transport layers for rapid one-to-many communications in large systems, OPC UA is able to leverage deterministic networks using Time-Sensitive Networking (TSN).
- IT-OT Integration
Companion specifications can be used to define applications and services available within IT systems, allowing their integration within a unified OPC UA architecture in exactly the same way as real word devices are modelled and accessed.
How does OPC UA do vs. other industry standards regarding cost/revenue?
Specifications, sample code etc. are all openly and freely available. No royalties to pay on any runtimes. Membership of the OPC Foundation is not necessary to access resources or certification labs. A modern IPR policy protects not only OPC foundation members, but also all adopters of OPC UA.
There is a level of complexity within OPC UA which means there appears to be a steeper learning curve than for some other technologies. In reality this is rarely the case because of the comprehensive nature of the specification. With other technologies users must factor in the learning curves of associated technologies needed in order to build a complete, end to end, secure, resilient, interoperable and open system. Once all of these parallel learning curves are considered, it can be seen that OPC UA is not any more complex or expensive to implement than any other system offering similar capabilities. Indeed, because features are already integrated into the specification, the overall effort required to implement an OPC UA based system can be considerably less than with other approaches.
What are OPC UA’s major applications?
OPC has its origins in the OT layer between smart devices such as PLCs and supervisory systems such as SCADA. Whilst OPC UA remains highly relevant in this area, the object based nature of the architecture mean that the real hotspot is in the interface to SOA based IT systems, which really benefit from the ability to group and define data by asset type, and the richness of the datasets it provides against these asset models.
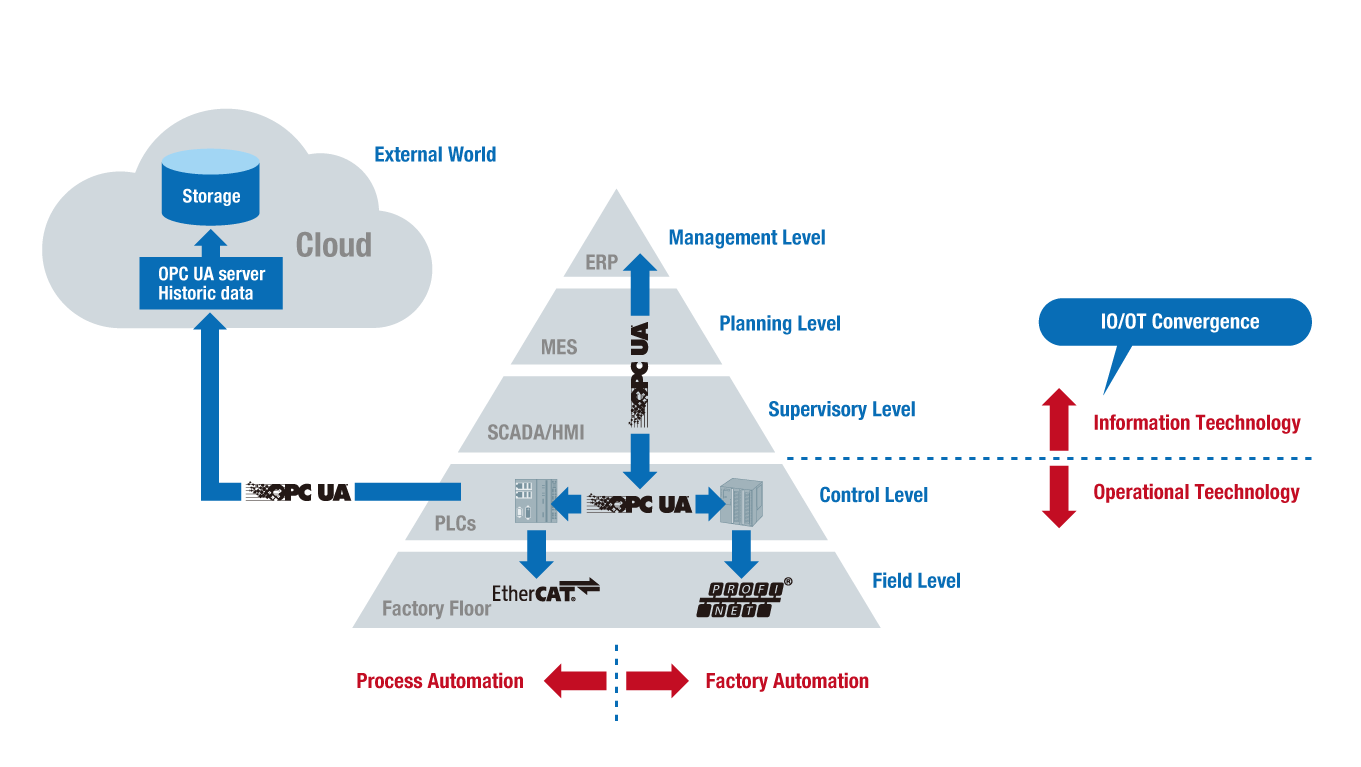
At the same time, OPC UA is significantly improving the ability for factory floor systems to communicate with each other in a peer-to-peer arrangement. This can significantly increase the efficiency of a production line by eliminating the delays associated with handing production process between machines, whilst also allowing machines that have otherwise incompatible fieldbus or protocol models to interact directly with each other.
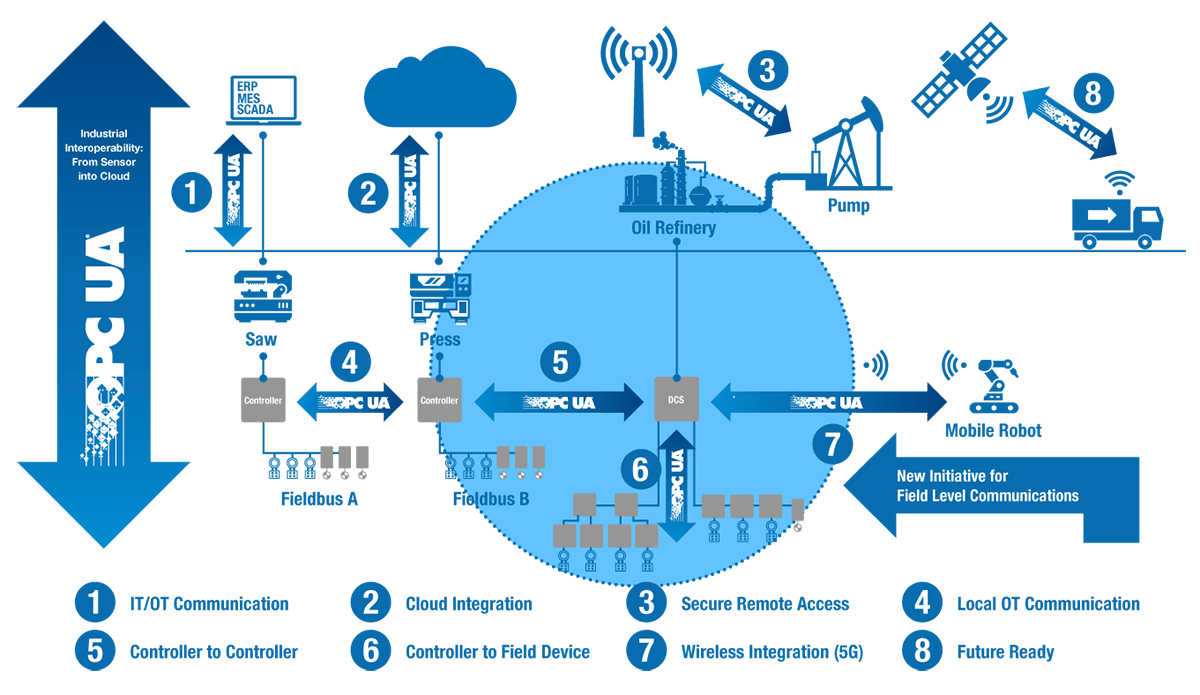
How widely adopted is OPC UA?
There are over 450 companies who are members of the OPC foundation. Hundreds more are developers or users of OPC technologies without being foundation members. Users come from OT, IT, academic and research backgrounds, and range from small independent software provides to large multi-national automation corporations. Collaboration groups exist to share resources, knowledge, and promote the OPC UA architecture and its related companion specifications.
What are the benefits of OPC UA Ethernet I/O vs. Modbus Ethernet I/O?
OPC UA Ethernet I/O provides a much richer datastream which allows its direct use in applications without prior knowledge. Modbus (P1 port) Ethernet I/O is compatible with older SCADA systems, but simply provides a stream of ‘1’ and ‘0’s, leaving the user to define and configure all of the information which contextualizes it. With Advantech OPC UA Ethernet I/O, you’re covered either way, as they provide support for both OPC UA and Modbus TCP.
How OPC UA enables and simplifies remote facility management?
Let’s start by analyzing the ideal needs of any system targeting remote management. Firstly it must be secure, to ensure that only authorized actors can interact with each other, and can see the data flowing between them. Secondly, it must have the versatility to work over a number of different communication topologies, including some which are subject to occasional dropout. Then, it needs to work with not just a single type of device from a single vendor, but instead with multiple device types from multiple vendors. It also needs to provide an easy way to contextualize the data that is flowing, ideally one which is machine readable rather than requiring human intervention of interpretation. Finally, it needs to interact with multiple systems, both from an IT and OT background. Of course, it is possible to address all of these elements by combining and integrating technology solutions from multiple sources, but OPC UA provides all of this within a single, open and publicly adopted standard. Simply by deciding to base a system architecture on OPC UA, all of these elements are intrinsically available ‘out of the box’, leaving users to concentrate on their application and value add, rather than the mechanics of building an infrastructure.
Why Advantech WISE-EdgeLink software is the optimal protocol gateway solution for OPC UA
applications?
Innovation in the industrial automation industry is often limited by the installed base of monitoring and control devices at the edge. Product lifecycles in the industry mean that these can often be ten or fifteen years old, relying on communication technologies and protocols prevalent at the time of installation. It is often impractical to replace all of these legacy assets when wanting to adopt new technologies. Advantech WISE-EdgeLink software provides the necessary bridge between them and modern systems based upon standards such as OPC UA, enabling users to migrate to take advantage of new innovations whilst protecting your investment.
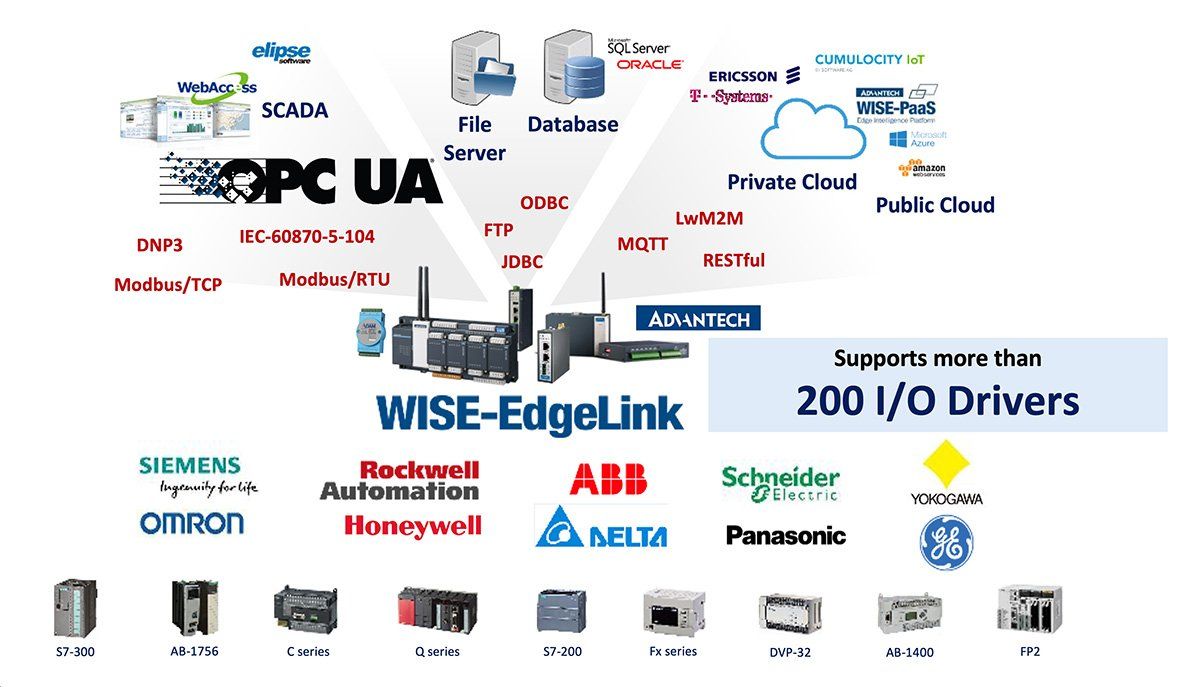
Advantech OPC UA Applications
An OPC UA Solution for Wastewater Treatment Monitoring System
Wastewater treatment requires an automated monitoring system to ensure that each and every one of the equipment units is operating in good standing and protects workers from exposure to pollutants or harmful chemicals. Advantech has been an important supplier for data acquisition modules and other products needed for building an intelligent SCADA system in many sewage treatment projects around the world. Our newest solutions supporting OPC UA will help reduce the cost of maintaining an IoT network and enhance data security from the field to the cloud.
ADAM-6300 : OPC UA remote I/O module
ICR-2431 : 4G/LTE cellular router
ICR-4453 : 5G router & gateway
ADAM-3600 : all-in-one intelligent RTU
MIC-710 : AI edge computer
WISE-EdgeLink : communication gateway software
OPC UA Enabled SCADA Monitoring Solution for Gas Stations
The operation of a gas stations involves a lot of automation and sensors for filling different vehicles with fuel. Any leaks of fuel into the air or the soil would not only undermine revenues but could also harm the environment and the health of workers at the station. Advantech’s ecosystem partner in the Middle East used our ADAM data acquisition I/O modules and an all-in-one intelligent remote terminal unit (iRTU) supporting OPC UA to realize a cost effective SCADA monitoring solution that delivered unparalleled data security.
ADAM-3600 : all-in-one intelligent RTU
ADAM-4000 : serial I/O module
ADAM-6200 : Ethernet I/O module
UNO-410 : explosion-proof computer
WISE-EdgeLink : communication gateway software
Advantech OPC UA Product Offerings
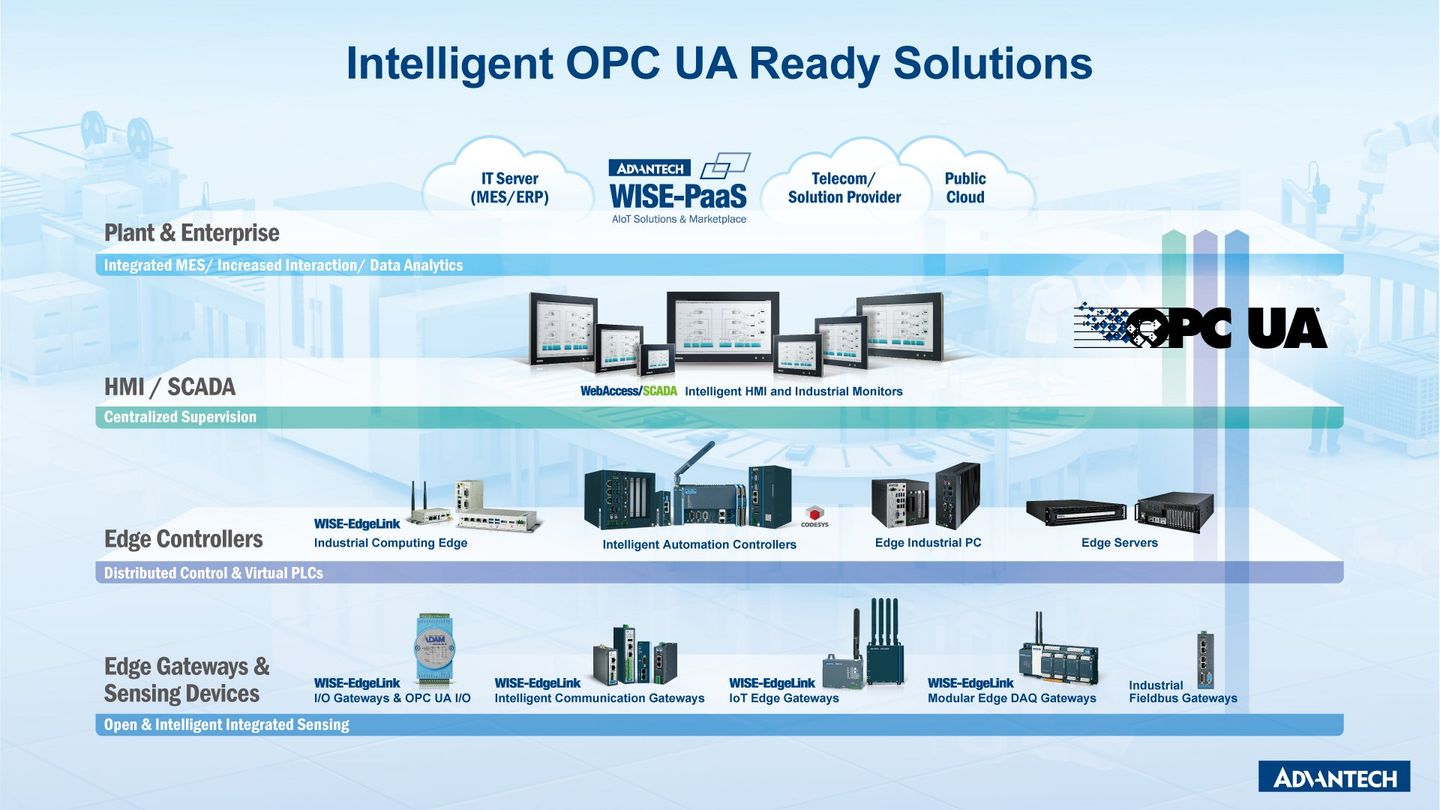
OPC UA Product Specifications
ESRP-CSS-UNO2484 | ESRP-CSS-UNO1372 | ESRP-F137 | ESRP-S238 | ESRP-S247 | OPC UA Products | ADAM-6300 | ESRP-PCS-ADAM6700 | ESRP-PCS-ADAM3600 | ESRP-PCS-ECU1051 | ESRP-PCS-ECU1251 | EKI-1242IOUMS | ESRP-PCS-ECU4553 | AMAX- 658 | AMAX-637 | ESRP-CSS-UNO2271 |
---|---|---|---|---|---|---|---|---|---|---|---|---|---|---|---|
Edge Gateway | Edge Gateway | Edge Gateway | Edge Gateway | Edge Panel | Product Types | Remote I/O Modules | I/O Gateway | I/O Gateways & RTU | Lightweight Gateway | Lightweight Gateway | Modbus to OPC UA Fieldbus Gateway | Edge Gateway | Codesys Controller & Fieldbus Gateway | Codesys Controller & Fieldbus Gateway | Edge Gateway |
Yes | Yes | OPC UA Server | Yes | Yes | Yes | Yes | Yes | Yes | Yes | Yes | Yes | Yes | |||
Yes | Yes | Yes | Yes | Yes | OPC UA Client | Yes | Yes | Yes | Yes | Yes | Yes | ||||
Yes | Yes | Yes | Yes | I/O Modules | Yes | Yes | Yes | Yes | Yes | ||||||
X86 | X86 | X86 | X86 | X86 | Hardware | MCU | ARM | ARM | ARM | ARM | ARM | ARM | X86 | X86 | X86 |
Linux | Linux | Windows/Linux | Windows/Linux | Windows/Linux | Operating System | non-OS | Embedded Linux | Embedded Linux | Embedded Linux | Embedded Linux | Embedded Linux | Embedded Linux | Windows | Windows | Linux |
Modbus | Modbus | EdgeX, Modbus, SNMP | EdgeX, Modbus, SNMP | EdgeX, Modbus, SNMP | Industrial Connectivity | OPC UA, Modbus/TCP | Modbus, BACNet, IEC-101, IEC-104 | Modbus, BACNet, DNP3, IEC-101, IEC-104 | Modbus, BACNet, DNP3, IEC-101, IEC-104 | Modbus, BACNet, DNP3, IEC-101, IEC-104 | Modbus | Modbus, BACNet, DNP3, IEC-101, IEC-104 | EtherCAT, PROFINET, EtherNet/IP, Modbus, Profibus, CANOpen | EtherCAT, PROFINET, EtherNet/IP, Modbus, Profibus, CANOpen | Modbus |
LAN, WiFi, Cellular | LAN, WiFi, Cellular | LAN, WiFi, Cellular | LAN, WiFi, Cellular | LAN, WiFi, Cellular | Network Connectivity | LAN | LAN | LAN, WiFi, Cellular | LAN/WIFI/Cellular | LAN, WiFi, Cellular | LAN | LAN | LAN | LAN | LAN, WiFi, Cellular |
Wall mount, DIN Rail | DIN Rail | Wall mount, DIN Rail | Wall mount, DIN Rail | Wall mount, DIN Rail | Form Factor | Wall mount, DIN Rail | Wall mount, DIN Rail | Wall mount, DIN Rail | Wall mount, DIN Rail | Wall mount, DIN Rail | Wall mount, DIN Rail | Rack mount | DIN Rail | DIN Rail | Wall mount, DIN Rail |
Codesys | Yes | Yes | |||||||||||||
Yes | Yes | Edgelink | Yes | Yes | Yes | Yes | Yes | Yes | - | - | Yes | ||||
Azure, AWS, MQTT | Azure, AWS, MQTT | DeviceOn/BI | DeviceOn/BI | DeviceOn/BI | Cloud Services | Azure, AWS, MQTT | Azure, AWS, MQTT | Azure, AWS, MQTT | Azure, AWS, MQTT | Azure, AWS, MQTT | MQTT (Sparkplug), ODBC | MQTT (Sparkplug), ODBC | Azure, AWS, MQTT |
Resources Download
Contact Us
Advantech Newsletter